When Picking and Sorting Tomatoes Become a Matter for Tech
- Posted by
Red Pitaya Team , August 18, 2023
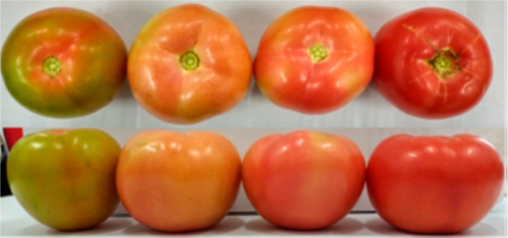
It’s funny how brands sometimes become visual references in their areas of expertise, as if they were the gold standard, a shorthand for quality. This seems to be happening to Red Pitaya boards, with designers often including the typical STEMlab shape in their experimental setup diagrams. Indeed, its exactly the distinctive shape and color of a Red Pitaya board that catch the eye when flipping through the Design of a Tomato Sorting Device Based on the Multisine-FSR Composite Measurement, a recent paper published by Zizhao Yang et al. (see the schematic diagram in Figure 1, with the STEMlab standing out on the lefthand side)
Figure 1 Schematic diagram bioelectrical impedance measurement
The paper describes a phenomenon that’s becoming ever more common: human skills that were once seen as impossible to automate now appear to be simple, although such developments are usually supported by significant technological prowess. Picking and sorting tomatoes, as well as other fruits and vegetables, is one such set of skills – a slow and strenuous manual process that can be taken over by technology, sparing people backache and increasing both productivity and efficiency.
Besides the mechanics of picking, defining a tomato’s ripeness is crucial when determining shelf life and quality. It seems only logical that tomatoes get sorted according to their ripening stage and stored or brought to the consumer based on this. Since this is slow and dull work for a human, engineers have been looking into ways of automating this task, and several solutions based on visual color recognition have been tested. Some drawbacks of this method include the fact it is impossible to analyze the internal condition of the tomato, and that it is sensitive to background light conditions. To overcome these issues, researchers from Nanjing Agricultural University in China have started experiments based on multifrequency bioelectrical impedance and force measurement. The impedance analysis not only makes it possible to define the ripeness or N2-content, but also to detect the presence of diseases and pests.
To perform the test, a number of tomatoes of the Suhong 50 variety were evenly divided into four ripening stages: green, white ripening, color transformation, and pink ripening, as can be seen in Figure 2.
Figure 2 Four tomato ripening stages (top and side views for each stage)
A rubber pneumatic end effector finger, visible in Figure 3, was developed for rotary picking. The rubber material was chosen because it reduces the damage to the tomatoes, compared to similar rigid picking claws. Each effector was equipped with two current injection and two voltage collector electrodes for multifrequency impedance measurement, and connected to the experimental setup (Figure 1) where we can see the STEMlab unit providing the excitation voltage, as well as picking up the resulting measurement signal for processing.
Figure 3 Rubber pneumatic end effectors, with integrated electrodes
The picking process consists of the effector approaching the tomato in an open state and enveloping it, after which the air duct is inflated, making the fingers bend inwards. While applying different forces (measured with an integrated Force Sensitive Resistor, or FSR), multifrequency impedance measurements are performed at four thresholds (4, 6, 8 and 10 N). These measurements result in an impedance curve with a particular shape, spiking at a frequency of around 5 kHz. An example of such a graph can be seen in Figure 4.
Figure 4 Tomato impedance vs. frequency at different forces, here in the green phase
In absolute terms, the impedance decreases as the ripeness of the tomato increases. Studying this in more detail, for an applied force of 10 N we can see the impedance at 5 kHz decreasing as follows: ~14 kW (green stage); ~13.5 kW (white ripening stage), ~12.3 kW (color transformation stage), and ~11.8 kW (pink ripening stage). This is shown in more detail in Figure 5.
Figure 5 Tomato bio-impedance at different ripeness stages
The results show that at an applied force of 10 N, the relative impedance error was below 5% in the frequency range 2-13 kHz. The time it took the STEMlab to collect and analyze the impedance measurements was around 0.6 s, with a recognition accuracy of around 95%, which is around 10 times faster and 2.5 percentage points more accurate than with visual systems. These are especially promising results for a low-budget setup, and we can´t wait to see this system – with the red STEMlab board standing out brighter than ever – integrated in real-life machines, picking and sorting away, and sending tomatoes to your plate in their optimum state.
Credits go to Zizhao Yang, Yongnian Zhang, Xiaochan Wang and Guangming Chen from the College of Engineering, Nanjing Agricultural University, Nanjing 210031, China, Ahmed Amin from the Agricultural Engineering Research Institute (AEnRI), Agricultural Research Center (ARC), Giza 12311, Egypt and Mahmoud A. Abdelhamid from the Department of Agricultural Engineering, Faculty of Agriculture, Ain Shams University, Cairo 11566, Egypt
You can read the full article here.