A Scanning Probe Microscopy Controller for Nano-Precision Surface Scanning
- Posted by
Red Pitaya Team , November 6, 2023
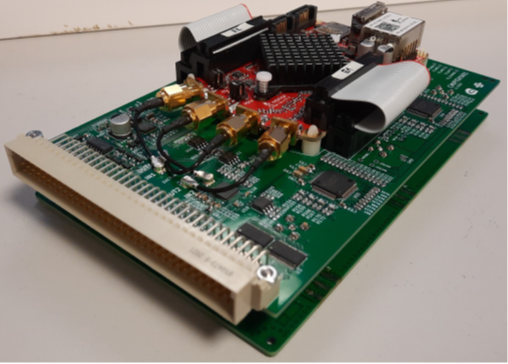
Scanning Probe Microscopy – or SPM – is a widely used scanning technique, providing surface topology maps at micro- and nanoscale. The general definition actually covers different types of technologies and physical phenomena, including Atomic Force Microscopy (AFM), Scanning Tunneling Microscopy (STM), Scanning Probe Electrochemistry (SPE), and so on. Operation modes include constant-interaction mode – adjusting the Z-position of the probe while moving it over the sample to maintain constant interaction between the probe and surface – and constant-height mode. The scanning point layout is usually defined in rectangular topography raster patterns, where this information is then combined with additional signals representing other physical parameters and sampled in the same scanning points as the topography.
This standard raster strategy results in an evenly distributed scanning resolution, with the risk of clogging your system with overly precise data for areas where a lower resolution would be sufficient, or missing valuable information in critical areas due to a lack of scanning density. Strategies have been developed to avoid this risk, including adaptive scanning – implementing non-raster patterns for data sampling that increase the resolution in critical areas – and multi-scale sampling for improved statistical properties. The article Scanning Probe Microscopy Controller with Advanced Sampling Support, published by M. Valtr et al. of the Czech Metrology Institute, describes the development and test results of a custom-built control system for adaptive SPM scanning that can be used with different scanning technologies. The paper also explains how adaptive scanning was simplified, using the Gwyscan library for non-raster scan path generation and adding a general XYZ-data handling support to the Gwyddion open-source software. To demonstrate the capacities of this system, an experimental hardware setup was developed using Gwyscan-generated scan paths and collecting data in a way that is compatible with general XYZ-data handling in Gwyddion.
Figure 1: DSP hardware setup: Red Pitaya, signal generation and acquisition framework
The setup hardware includes a Digital Signal Processor (DSP) for SPM, capable of generating X-Y scan positions, communicating these to the piezo amplifier, maintaining a feedback loop between probe and sample, driving AC signals and performing lock-in detection, communicating with the microscope user interface, and running Lua scripts for autonomous scanning. It consists of two independent parts: the feedback loop module, implemented in a Red Pitaya STEMlab 125-14 unit, and the signal generation and acquisition framework, including two electronic boards with 16-, 18-, and 20-bit resolution channels. The DSP functionality is provided by a single C-language API, allowing remote client-server operation via Ethernet connection.
Different feedback loops are implemented on the STEMlab’s FPGA, using a custom-built bitstream that allows constant-interaction mode operation. The 2-channel 14-bit ACD of the Red Pitaya unit, running at the traditional 125 MS/s sampling rate, provides the main data source for the loop. This sampled data can be used directly or passed through two independent lock-in amplifiers. The main feedback loop supplies Z-position feedback for SPM measurements, while other feedback loops can be used for phase-locked loop feedback.
The two PCBs, constituting the signal generation and acquisition framework, enhance the STEMlab capacities. They are equipped with multiplexers that communicate with the Red Pitaya board via the SPI interface and allow 16-, 18-, and 20-bit resolution operation.
The functionality of the hardware is controlled using a dedicated C-library, providing an API for all operations and allowing the creation of an Ethernet communication interface server for remote user setup of the microscope control software. Features for adaptive and non-raster scanning include: X-Y coordinates and timestamp of all scanned data; server loading and scanning of scan paths, precomputed with the Gwyscan library; and adaptive scan path creation and advanced statistical functions using the Lua scripting interface.
This results in a low-cost DSP with high bit-depth ADCs and DACs, capable of performing all typical SPM operations, providing data compatible with the general XYZ-data processing framework in the Gwyddion open-source software.
Two experiments were run with this experimental SPM DSP, using two different hardware setups. The first one was based on a custom-built conventional AFM head, the second one on Piezo-Resistive Sensing & Active (PRSA) probes. Both systems were tested and compared to a commercial state-of-the-art SPM.
Figure 2: Scanning results of two experimental setups
Validation tests were performed on two silicon step samples – used for calibrating the vertical microscope axis – for evaluation of the noise levels and overall performance of the SPMs. The following test results are shown in Figure 2: A) AFM scan of a silicon step sample; B) commercial SPM scan of the same part; C) PRSA scan of a second step sample; D) commercial SPM scan of the same part (the white spots correspond with dust particles on the silicon samples). The results show a noise level around 225 pm for the custom-built AFM system, and below 100 pm for the mechanically optimized PRSA system, meaning that the low-cost DSP, described in this experiment, can achieve a performance comparable to those of commercial state-of-the-art microscopes.
Low-cost, high performance, Red Pitaya: the three terms seem inseparable when trying to summarize this experiment, as with so many others before. Building systems with COTS elements and delivering a performance equivalent to those of commercial devices is embedded in the STEMlab DNA, as is Red Pitaya’s continuous quest for improvement. Although 18- and 20-bit resolutions may still seem far away, so was the 16-bit version only a couple of years ago. So it’s easy enough to imagine a similar system without the need for additional hardware that’s able to reach this level of performance, and we at Red Pitaya look forward to being part of the story.
Source: www.ncbi.nlm.nih.gov